Fastener Assembly Galvanic Corrosion Testing
As a further assessment, several 316 stainless steel screws and washer assemblies were prepared bare, and separately coated with Gentoo. The fasteners were attached to primed and topcoated aluminum alloy 7075-T6 (UNS A97075) coupons and exposed to accelerated corrosion conditions for galvanic corrosion assessment. Specifically, the fastener assemblies consisted of ¼-20 x 1 inch full-thread screws and corresponding mated flat washers (Figure 6), with and without Gentoo.
Select screws and washers were also cadmium plated per ASTM F1941 FE/CD 5A. The 7075-T6 aluminum coupons were approximately 1 x1.375 x0.032 inch and a ¼-20 drill and tapped hole was created in the middle region of each one for mated fastener attachment. All aluminum panels were initially deoxidized with Alumiprep 33 and treated with PreKoke, a non-chromate adhesion promoter for paints. Following the pretreatment, a MIL-PRF-23377 epoxy primer and MIL-PRF-85285D grey polyurethane topcoat from PRC Desoto were applied to the surface.
The coated coupons were hand-scribed to expose fresh, bare metal prior to fastener attachment. During galvanic assembly, nylon spacers and 18-8 stainless steel nuts were used on the backside of the aluminum coupons and torqued to 25 in-lbs. Each distinct assembly type was tested in triplicate via placement in ASTM B117 cyclic salt fog conditions.
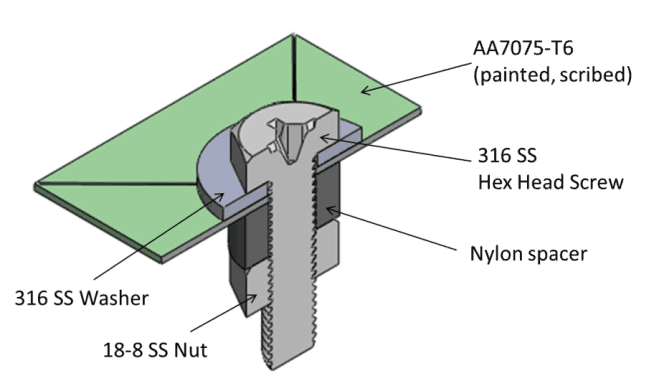
Figure 6: Schematic overview of the galvanic fastener assembly components used for corrosion assessment of Gentoo as applied to 316 stainless steel fasteners.
Bare B7 steel fastener and cadmium (Cd) plated B7 steel fastener assemblies were used for galvanic coupling with the scribed, painted aluminum panels. Control and Gentoo coated fastener assemblies were used. After 648 hours of B117 exposure, significant amounts of corrosion product was evident with the bare B7 steel fastener assemblies, while significantly less corrosion was evident after 1340 hours of salt spray with the cadmium plated B7 steel fasteners.
The test assemblies were removed from B117, solvent stripped and cleaned using ASTM G1 guidelines and evaluated for weight loss and pit depth measurements due to corrosion. The parts were solvent stripped by first using a Rust-Oleum Aircraft Paint Remover soak at 49°C, followed by immersion in a 60-70% nitric acid stripping solution and rinsed with ethanol to remove any residue.
Improved corrosion resistance from Gentoo treatment of fasteners and painted panels were demonstrated visually, by corrosion based weight loss and pit depth measurements of the stripped aluminum panels on both the bare B7 and cadmium plated B7 fastener assemblies. The barrier effect of the Gentoo appears to be potentiated when combined with electrochemically deposited layers, such as Cd plating. Results are displayed in Figure 7.
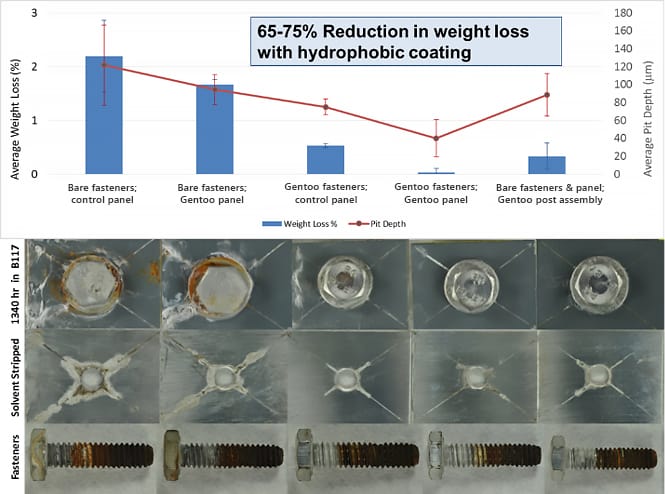
Figure 7: Galvanic Fastener Assembly Test Images of Cadmium plated B7 HSS bolts after 1340 hours of Salt Spray (top row images) and solvent stripped using ASTM G1, coated 7076-T6 aluminum panels (middle row) measured for weight loss and pit depth (accompanied graphs), and side images of representative fasteners (bottom row)