Corrosion Resistance
In this section and the following sections outlined in the Test Data Index menu, continuous salt fog corrosion resistance, chipping resistance combined with salt fog corrosion resistance, and galvanic and HSS accelerated corrosion resistance and environmental exposure at Kennedy Space Center in Florida results are reported in detail. Performance evaluations focused on LHE ZnNi plated 300M (UNS K44220) or 4130 (UNS G41300) high strength steel parts. All HSS threaded parts were 300M, while all HSS flat panels were 4130 alloy. All testing was performed in triplicate. Specific testing procedures are discussed in the results section.
Accelerated ASTM B117 corrosion testing was performed on LHE Zn-Ni plated 4130 HSS painted panels. The flat panels were primed with a MIL-PRF-85582 Class N chrome-free epoxy primer and topcoated with a CA8201/F17925 MIL-PRF-85285 Type I Class H white glossy urethane paint, or a CA8211/F3673 MIL-PRF-85285E Type I grey semi-gloss paint.
Control panels included the primer and topcoats only. Gentoo was applied to selected control panels. All panels were “X” scribed according to MIL-PRF-32239 and placed in ASTM B117 salt fog with images taken every 500 h. Figure 8 displays the salt fog exposed panel images for the white and grey topcoat controls and Gentoo treated panels.
Significant amounts of red rust are present on all the panels with the onset of rust by 500 h of exposure. The scribe corrosion is rated according to ASTM D1654 for each of the panels and is graphically displayed in Figure 9. For both the white and grey topcoats, the Gentoo treatment significantly reduces the scribe creep.
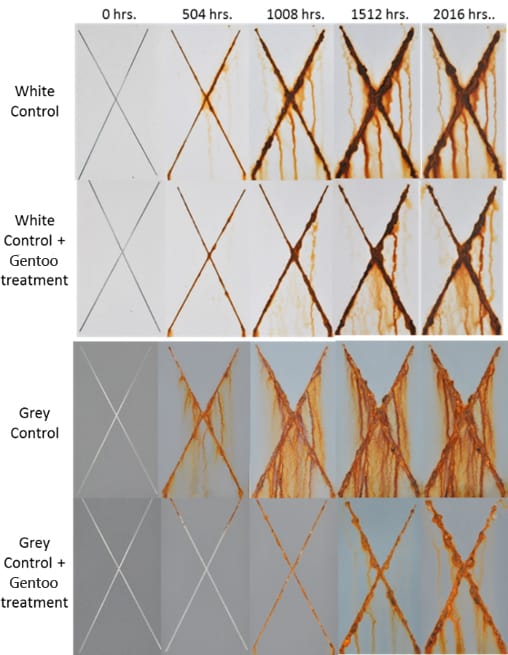
Figure 8: Images of MIL-PRF-32239 scribed LHE Zn-Ni 4130 HSS painted panels with either the MIL-PRF-85285 white glossy topcoat or the MIL-PRF-85285 grey semi-gloss topcoat with and without Gentoo following ASTM B117 Salt Fog Exposure
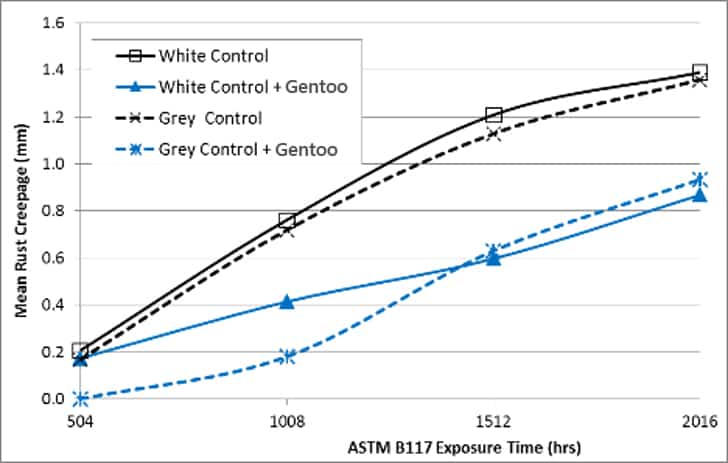
Figure 9: ASTM D1654 Scribe Corrosion Ratings of Scribed, ASTM B117 Salt Fog Exposed painted, LHE Zn-Ni 4130 HSS panels with and without Gentoo